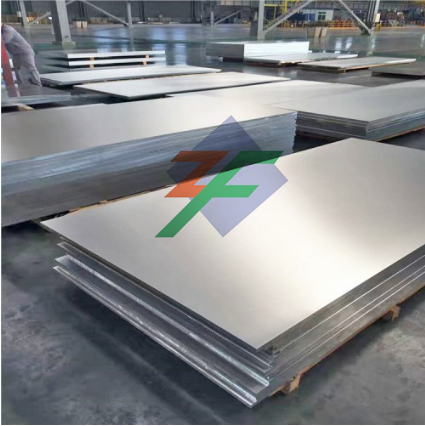
The density of aluminum plates refers to their mass per unit volume, typically measured in grams per cubic centimeter (g/cm³). Aluminum, as a metal, has a relatively low density compared to iron, copper, or steel. This low density is one of the key reasons aluminum plates are preferred for lightweight applications where reduced weight is critical, such as in aerospace, automotive, and construction industries.
The density of aluminum plates can vary depending on the alloy composition and the manufacturing process. Common aluminum alloys used for plate production include 1050, 1060, 3003, 5052, and 6061. These alloys offer a range of properties tailored for specific applications, from pure aluminum's excellent corrosion resistance to alloys reinforced with other elements for increased strength.
The low density of aluminum plates translates into several advantages. Firstly, it reduces the overall weight of structures and components, leading to improved fuel efficiency in vehicles and reduced structural loads in buildings. Secondly, aluminum's lightness makes it easier to handle and install, reducing labor costs and enhancing work efficiency. Finally, the low density combined with aluminum's excellent formability allows for the creation of complex shapes and structures that are both lightweight and structurally robust.
In addition to its low density, aluminum plates also exhibit good thermal conductivity, electrical conductivity, and resistance to corrosion. These properties further enhance their versatility and make aluminum plates suitable for a wide range of applications, including heat exchangers, wiring systems, and exterior cladding.
In conclusion, the low density of aluminum plates is a crucial factor contributing to their widespread use in various industries. Their lightweight properties combined with excellent formability and corrosion resistance make aluminum plates an ideal material for creating structures and components that require both strength and lightness.